Case Study

Consolidating Procurement Processes
Background
Absolute Quality Manufacturing (AQM) is a leading provider of cable harnesses and control panel with manufacturing solutions optimizing production processes for efficiency and quality. AQM approached the client, a large OEM company, offering resources to collaborate in improving their operations to save time, reduce waste, and enhance overall productivity.
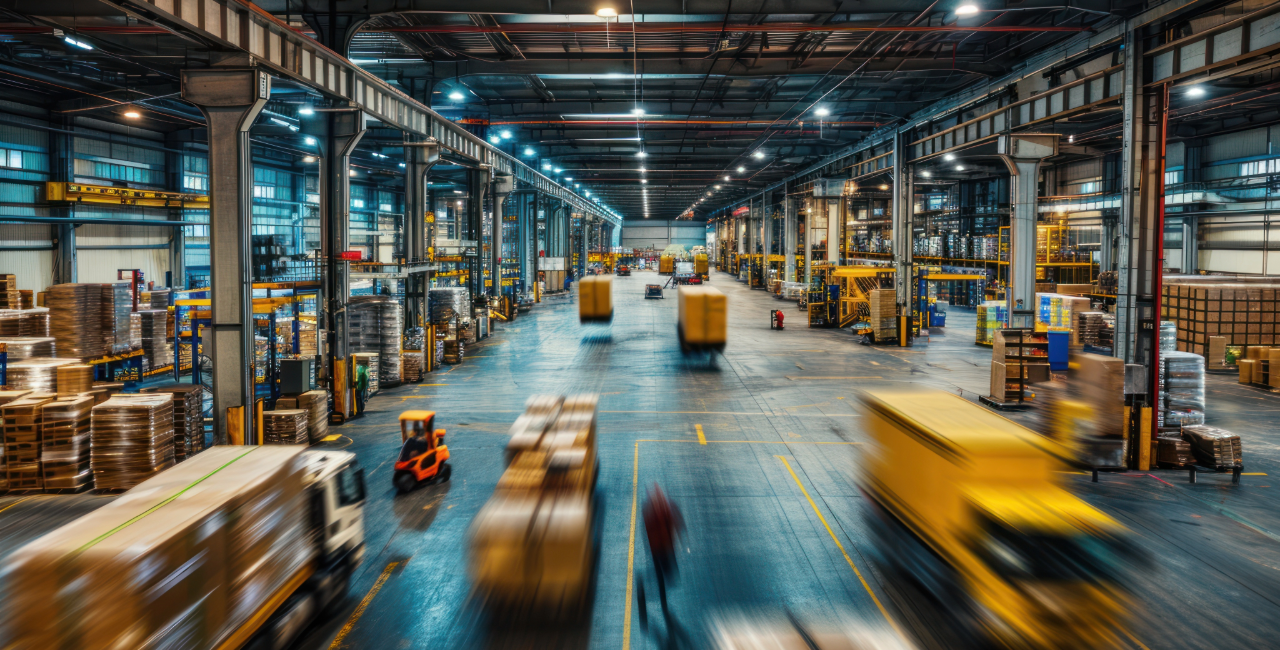
Challenge
In today’s competitive business landscape, operational efficiency is paramount for success. For one of our clients, managing a multitude of purchase orders across various vendors was proving to be a significant challenge, leading to inefficiencies and increased administrative burdens. Seeking a solution to streamline their procurement processes, they turned to Absolute Quality Manufacturing (AQM) for assistance.
HIGH PURCHASE ORDER COUNT
The client had to manage 33 separate purchase orders for various components, including custom cables, from different vendors.
LACK OF DEDICATED ACCOUNT MANAGEMENT
With multiple vendors, the client did not have a single point of contact who understood their business needs thoroughly.
INVOICING COMPLEXITY
Managing invoices from multiple vendors led to complexity and increased administrative overhead.
FRAGMENTED SUPPLY CHAIN
Dealing with numerous vendors resulted in a fragmented supply chain, making coordination and communication challenging.
Solution
AQM recognized the need for a comprehensive solution to address the client’s challenges effectively. Leveraging its expertise in custom cable manufacturing and the vast network of franchised lines maintained by Stark Electronics Inc., AQM proposed a consolidated approach to streamline the client’s procurement processes. The key components of the solution included:
CUSTOM CABLE SOURCING
AQM collaborated closely with the client to understand their specific cable requirements and provided tailored solutions to meet their needs. By sourcing custom cables from AQM, the client could ensure quality, precision, and reliability in their products.
LEVERAGING STARK ELECTRONICS NETWORK
Through Stark Electronics extensive network of franchised lines, the client gained access to a wide range of electronic components and peripherals. This allowed them to consolidate their component purchases along with custom cables, simplifying the procurement process.
DEDICATED ACCOUNT MANAGEMENT
AQM assigned a dedicated account manager to the client, serving as a single point of contact for all their procurement needs. The account manager developed a deep understanding of the client’s business requirements, ensuring personalized service and proactive support.
STREAMLINED ORDER MANAGEMENT
By consolidating purchases through AQM and Stark Electronics Inc., the client significantly reduced the number of purchase orders they had to manage, streamlining their order management processes.
CONSOLIDATED INVOICING
AQM provided consolidated invoicing for all purchases, eliminating the need for the client to manage multiple invoices from different vendors. This simplified their accounting processes and reduced administrative overhead.
results
The implementation of AQM’s solution yielded significant benefits for both AQM and the client:
1. Time Savings: The client experienced a remarkable reduction in production, packaging, and shipping times, saving approximately 40 hours per week. This allowed them to fulfill orders more efficiently and respond quickly to changing market demands.
2. Operational Efficiency: AQM also saved 30 hours of time internally through improved processes and streamlined workflows. This freed up resources to focus on innovation and further improvements.
3. Waste Reduction: The implementation of lean manufacturing principles and innovative packaging solutions led to a substantial reduction in waste generation across the entire supply chain. This not only minimized environmental impact but also resulted in cost savings for the client.
4. JIT Implementation: By adopting Just-in-Time manufacturing practices, the client significantly reduced inventory storage needs and eliminated excess stockpiling. This freed up valuable warehouse space and reduced holding costs.
REDUCED PURCHASE ORDER COUNT
The client’s purchase order count decreased from 33 to one, leading to greater efficiency and reduced administrative burden.
ENHANCED ACCOUNT MANAGEMENT
With a dedicated account manager from AQM, the client received personalized service and proactive support, leading to improved communication and collaboration.
SIMPLIFIED PROCUREMENT PROCESSESS
Consolidating purchases through AQM and Stark Electronics Inc. simplified the client’s procurement processes, saving time and resources.
FEWER VENDORS
By consolidating purchases, the client reduced the number of vendors they had to deal with, leading to a more streamlined supply chain.
CONSOLIDATED INVOICING
AQM’s provision of consolidated invoicing further simplified the client’s accounting processes, leading to cost savings and improved financial management.
conclusion
Absolute Quality Manufacturing’s tailored solution enabled our client to streamline their procurement processes, reduce administrative overhead, and achieve greater efficiency in their operations. By leveraging AQM’s expertise in custom cable manufacturing and Stark Electronics Inc.’s extensive network, the client benefited from simplified order management, consolidated invoicing, and dedicated account management. This case study exemplifies AQM’s commitment to delivering value-added solutions that drive operational excellence for its clients.
Similar case studies
Streamlining Processes & Saving Time
Supporting Struggling Labor Needs
We demonstrated unparalleled flexibility and adaptiveness in supporting a crucial OEM customer in the aftermath of a natural disaster. By deploying a dedicated team, replicating assembly lines, and assuming full manufacturing responsibility, AQM ensured timely generator production, aiding in disaster recovery efforts.
Reverse Engineering Rescue
Absolute Quality saved the day with a leading entertainment client in distress over 30-year-old cable assemblies crucial for a nationally televised event, AQM’s innovative solutions and swift action ensured success, showcasing our commitment to excellence and customer service.